What Makes Rotary Pump Different from Other Pump Variations
- vestrainet
- Aug 10, 2020
- 2 min read
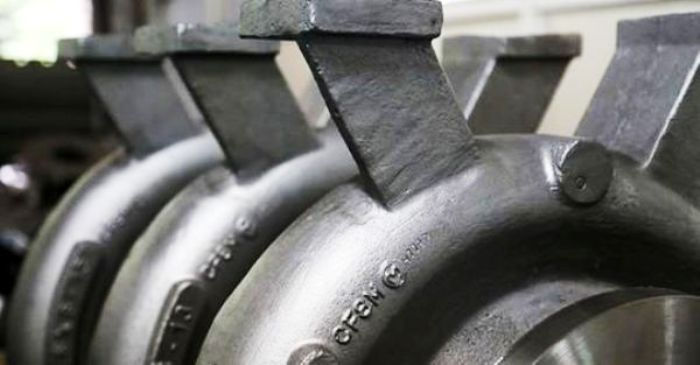
An industrial vacuum pump is a machine that removes gases from an enclosed space for the purpose of creating a vacuum. It comes in many different types and is used in a wide range of industries such as pharmaceutical, food and beverage processing, oil and gas, power generation and more. The most common type extensively used is the rotary pump due to its versatility, compact design, ability to deal with high differential pressure, high-viscosity performance, and continuous flow despite differential pressure.
Essentially, a rotary pump is a form of positive-displacement pump that displaces a known quantity of liquid with every revolution of its pumping components, including gears, lobes, vanes, rotary pistons, and screws. It traps fluid in a closed casing and discharges a smooth flow afterward and can handle almost any kind of liquid which does not have abrasive solids. When it comes to pumping highly viscous liquids, rotary pumps should be operated at reduced speeds to facilitate its flow into the casing fast enough.
Compared to a centrifugal pump, a rotary pump delivers a capacity that is not greatly affected by pressure variations on both the suction and discharge points. Rotary pumps are also self-priming, making them more advantageous to use than centrifugal pumps. Moreover, as a positive-displacement pump, a fixed amount of fluid or liquid can also be moved despite of the resistance against which the rotary pump is forcing. However, any clog in the system can instantly damage the pump or the entire system.
Therefore, the operator must make sure that the system is well aligned so that a complete, unobstructed flow path is ensured for smooth fluid flow. Finally, a rotary pump will need a relief valve to protect the piping system and prevent any undesirable accidents that can damage the equipment and the surrounding environment.
Comentários