What Makes Metal Fabrication A Success
- vestrainet
- Dec 16, 2020
- 2 min read
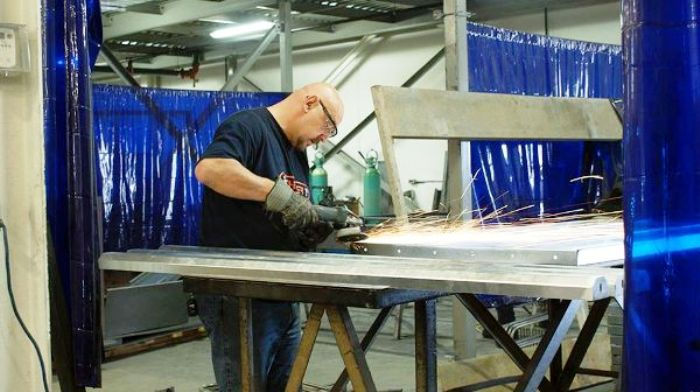
Sheet metal fabrication may appear like a big task and it will most likely be, depending on the specific metal component to be fabricated. Essentially, the process of metal fabrication involves cutting and forming a sheet of metal into the desired shape. The final metal parts or products fabricated can then be utilized for all kinds of projects, be it a simple home improvement project or a more complicated commercial structure project. The key for any sheet metal fabrication to become successful is precision and just like the other industrial processes, it is important to know the do’s and don’ts to achieve the best results.
The very first factor that the fabricator has to consider is the different properties of the sheet metal that has to be created according to its intended use. One of them is the thickness of the finish and the shape of the final product. For example, even a thin aluminum with a bend or more can be fabricated into shelves as long as the load it will carry has been taken into account. It can also make a perfect addition to either the kitchen or bathroom to give it a unique, modern feel. However, most of the time, sheet metal fabrication is more beneficial in creating metal parts for food processing industries, manufacturing elevators, escalators, and even for custom settings for the film industries.
Another crucial element that has to be considered for successful metal fabrication is the formability of the part. Various types of metals have different properties, particularly when it comes to bending and assembling parts together. Though stainless steel can be bent and welded, it’s great to use for decorative and hygienic purposes such as the case of food processing. Moreover, every metal has its own special characteristics that may affect the way how parts can be shaped. Yet, despite these specialties or unique properties, the specialists of 4 Way Metal can fabricate any shape and size in the way you want it.
Comments