What Determines the Right Selection of Conveyor Oven?
- vestrainet
- Dec 10, 2020
- 2 min read
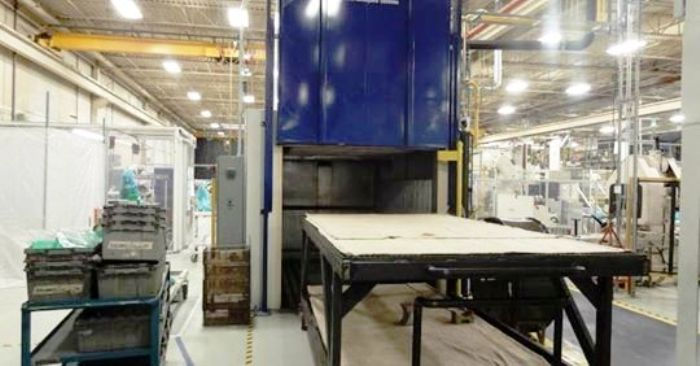
If you are wondering how conveyor ovens work, then you have come to the right place because we will be covering the basic information about this industrial oven. During the drying or heat treatment process, a conveyor oven usually uses a perforated belt to transfer the feed materials. The heated air is then passed below through or over the belt prior to being re-circulated. Moreover, the ovens are typically scattered in different zones and may have various airflows in the succeeding heat zones. It is also important to note that every zone may utilize a varying temperature profile and control.
Additionally, conveyor ovens can also come in multiple pass units. This means the feed is moved from one belt to another through gravity. These ovens are normally composed of two or more pass machines. Each of them is particularly designed and built according to the unique requirements of the customer’s process. Usually, they include various elements such as multiple heat zones, special belt constructions, cooling zones, and extended loading and unloading zones. All these components work together in enhancing the performance of a conveyor oven. However, you need to know how to properly size the length of your conveyor oven.
In order to know which among conveyor ovens is the most appropriate for your certain application, simply calculate the length of the heated tunnel. Just take note that the conveyor oven belt is sized depending on part dimensions, dwell time, as well as production rate. The width of the belt is chosen to accommodate the required loading pattern, be it side by side or inline. Various factors affect the design belt speed, including production rate, the equipment’s loading density, and the number of components per foot that can be accommodated. Lastly, you need to understand the connection between various elements, particularly the heat zone length, belt width, and production rate.
Comentarios