Understanding the Hobbing Process in Manufacturing Spline Shafts
- vestrainet
- Sep 28, 2020
- 2 min read
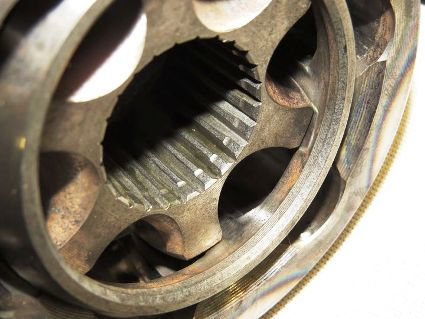
Hobbing is one of the widely used machining processes in creating different ridges or teeth on spline shafts. Furthermore, the ability of hobbing machines to cut accurately is one of the reasons why hobbing is valued in manufacturing splined shafts.
In today’s post, let’s see how the hobbing process can successfully create splines.
Splines are created using horizontal hobbing machines
Horizontal hobbing machines are specifically used for longer pieces like spline shafts. The horizontal orientation allows the hobbing tool to move easily from left to right or vice versa.
The unwanted parts are cut from the rotating work piece
The rotating cutter called the hob progressively cuts the grooves or teeth into the work piece until the desired tooth configuration is achieved. The cutting edges work simultaneously which results in fast cutting speeds and short cycle times.
The perfect hobbing tool for the job
Usually made of carbide, the hob is cylindrical in shape with helical cutting teeth. The right hobbing tool creates the desired tooth size and angle of the spline. Specifically, involute spline hobs are made with single or multiple thread designs and can have pressure angles of 30°, 37.5°, or 45°.
Wet hobbing machine uses the right cutting fluid
The hob should perform at its best so it can cut precise splines every time and fit with their mating component. For this reason, cutting fluids are a must for every wet hobbing process. They are used in hobbing machines to enhance lubricity, inhibit bacteria growth and prevent rust. Specifically, water-based fluids can effectively remove heat than oil.
Indeed, the hobbing process is one efficient machining process in creating spline shafts. Its horizontal orientation is perfect for handling long work pieces while its many cutting edges shorten the whole process.
Comments