Tips to Get the Best Results with Aluminum Welding Fabrication
- vestrainet
- Oct 19, 2021
- 2 min read
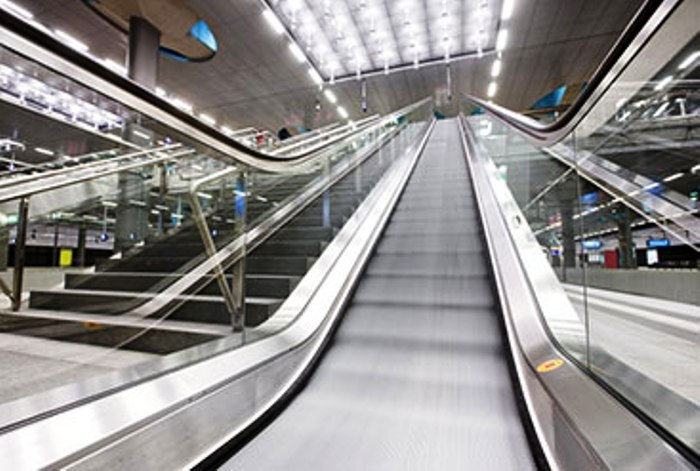
It can’t be denied that aluminum is such a great metal that has been used for a lot of applications across industries. However, working with aluminum during welding fabrication in Toronto will not always be easy and safe. With this in mind, we are giving you the following safety tips on how to deal with this metal.
Understanding aluminum
What makes aluminum unique from other metals is its high thermal conductivity, meaning the heat can spread all throughout the metal. This means compared with steel, the travel speed when welding aluminum can be much faster. Also, it helps to know that it is a porous metal with a melting point at around 1,221 F.
Removing the oxide layer
In order to remove the oxide layer off aluminum, it is advised to use wire brush made from either copper or brass wire because steel wire can further contaminate the metal. As you are wiring the aluminum, you would notice that it begins to look dull which is good as it means the oxide layers are breaking up. Also, do the wire brushing in one direction only to achieve better results.
Cleaning aluminum
One aspect you should know about aluminum is that it is very sensitive to contaminations. This means when cleaning the metal, you have to be very careful about the materials you use in cleaning. Common practice is wiping down the case material and filler rod with acetone or alcohol first. Moreover, if you are welding aluminum on a steel work surface, ensure that there’s no metal shavings on the table to avoid marks.
Right angling is crucial
Torch angle is another key to successful welding fabrication in Toronto that involves aluminum. This is because the filler rod has the tendency to ball up really fast even prior to dipping it. So, make sure that the welding torch used is at the right angle of 90 degrees or as close to vertical as possible.
While these seem to be much, practice will make everything a lot easier along the way and welding aluminum will now be a simple and safe task.
コメント