The Top Five Processes Involved In Custom Metal Fabrication Toronto
- vestrainet
- Jan 7, 2022
- 2 min read
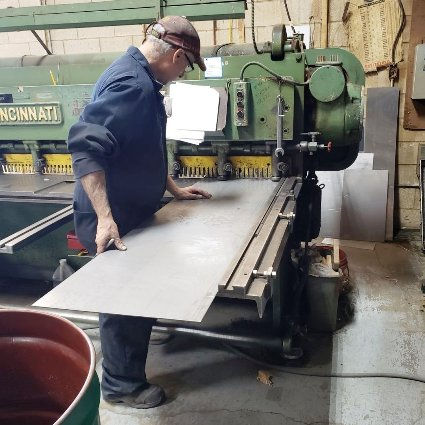
Metal fabrication is a broad term that is used to mean processes that cut, shape, or mould metals into a final product. Rather than assembling ready-made parts to create an end-product, custom metal fabrication in Toronto makes a final product from raw or blank materials. There are various fabrication processes involved during this project when creating stock and custom products. Here are the five of them, among many others.
Machining
This metal fabrication process refers to shaping metal by removing unwanted material from it. Machining can be done in a variety of ways, such as drilling, turning, and milling. Drilling involves the use of a cutting tool to make a hole in the material while turning is using a lathe and a cutting tool that removes metal along the diameter, creating a cylindrical shape. Milling is performed by feeding the material into a rotating tool to progressively remove material from the workpiece until the desired shape is achieved.
Cutting
The most widely applied cutting technology for custom metal fabrication in Toronto is laser cutting. Other cutting methods include sawing, waterjet cutting, plasma arc cutting, and using power scissors. Each of those cutting methods produces varied results. Selecting the right one depends on your project specifications. Usually, it may be the first stage in the entire metal fabrication process or the only process used.
Casting
This process is done by pouring the molten metal into a die or mould, allowing it to cool and harden into its desired shape. Casting is great for custom projects that require a number of parts using the same mould to produce identical parts. There are also multiple types of casting. Die-casting is the most common one in which a die is used instead of a mould. On the other hand, permanent mould casting is used when pouring the liquid metal into a mould.
Folding
Folding involves the manipulation of metal to bend at an angle using a brake press. The material is being held between a punch and a die and then forced to crease with pressure from the punch. Thus, it is often chosen to shape sheet metal to create a custom product design. It is done by hammering the material using a folder, or a folding machine.
Forging
Custom metal fabrication in Toronto also largely benefits from forging which is used to shape metal using a hammer or a die. Forging is often performed in metal at room temperature which is called cold forging. Conversely, warm forging is done in metal that is heated to a temperature that is above room temperature. Forging is one of the oldest processes of custom metal fabrication, which blacksmiths used centuries ago.
These are just some of the many processes involved in completing custom metal fabrication projects. Continue browsing our site to learn more.
Comments