The Great Technology Behind Gear Shaping
- vestrainet
- Aug 13, 2020
- 2 min read
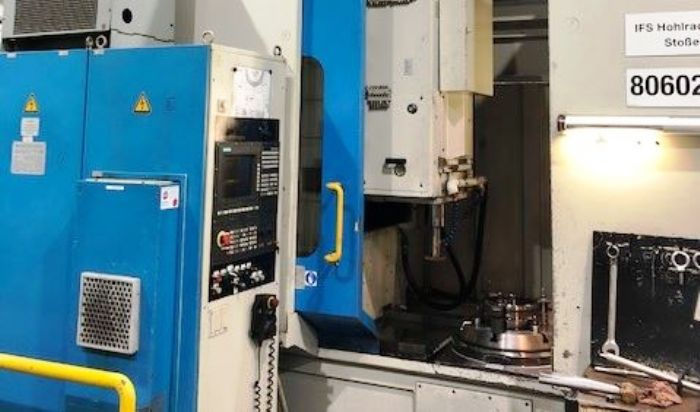
Gear shaping is a commonly used method to produce spur gears. While gear hobbing is found to be more efficient in cutting the workpiece simultaneously, which reduces changeover time, it is not suitable for machining of internal teeth of gears or in cases where there are obstructions in the region of the gear. This is why gear shapers are invented to machine a stepped gear that a gear hobber can’t accommodate.
Typically, the pinion cutter and the workpiece rotate harmoniously through a set gear ratio during the gear shaping process. However, this may cause a big variation in the cutting region for every stroke in machining the tooth of spur gears. This further results in producing a cutting force that is lower than the rated capacity of a gear shaping machine, thus reducing the efficiency of the gear shaper and the entire process.
The good news is that True Gear and Spline had addressed this problem by investing in the latest technology in gear shaping machines that are all capable of enhancing the process efficiency. All of our ST series of Mitsubishi CNC gear shapers are equipped with the advanced programmable lead guide that integrates high precision and high-speed control technologies, enabling spindle movement based on the helix angle of the gear cutter. This allows us to achieve the flexible production of external and internal helical gears in addition to spur gears.
All four Mitsubishi CNC gear shapers we use, with internal capacities of 400 mm to 760 mm, allow us to shape taper and crown gears and producing them with higher added value. We get the same reliable and efficient results with our Gleason CNC gear shaper, the Pfauter PSA 500, which provides 500 mm capacity. On top of all these systems is our advanced Wire EDM machine that is capable of processing multiple types of shapes including spur gears, splines, keyways, and many others. So, if you have any gear shaping requirements, just call us to get the best results.
Комментарии