Key Factors To Consider When Buying Air Compressor
- vestrainet
- May 26, 2021
- 2 min read
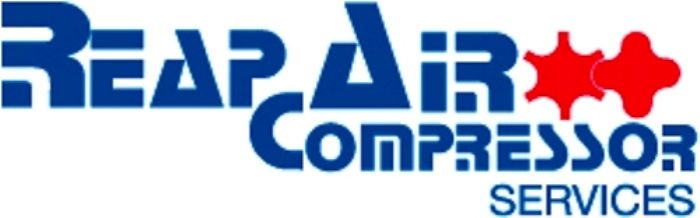
Most machinery and tools used within industrial settings are powered through the use of compressed air. The process in how an industrial air compressor operates is that they take in huge amounts of air and pressurize it via compression. The compressed air is then released via a hose that is connected into different tools, powering them for any purpose.
As industrial air compressors are not simple machines, they are quite expensive to purchase. Hence, it is important that you do your research first before buying a unit so that you can properly select the right one that best suits your requirements. Speaking of which, here are some of the major factors you have to consider during your selection.
Cubic feet per minute: also known as CFM, this factor refers to the amount of air that moves through the compressor unit. Always remember that a higher CFM is required if you have several tools to be powered by compressed air at the same time.
PSI: this one refers to the amount of pressure, pounds per square inch, generated by the industrial air compressors. Each pneumatic tool needs a different PSI and each unit has a maximum amount of PSI that can be produced.
Power source: this simply refers to the type of power you would like for the compressor. Would it be via electricity or gas? You have to decide on this as well.
Filters: these elements might be very simple but they perform a crucial role in removing and trapping airborne contaminants that can cause harm to your compressed air system.
Air coolers or dryers: most of the industrial air compressors are contending with condensation that may form inside your equipment which can bring serious problems. This is where air dryers come to prevent condensation from happening.
Keep in mind these important factors when selecting the right air compressor for your application. And of course, don’t forget to get your equipment only from a reliable supplier with the right knowledge and expertise in the field.
Comments