How to Deal with Bearing Clearance in Helical Gear Motors
- vestrainet
- Jan 26, 2021
- 2 min read
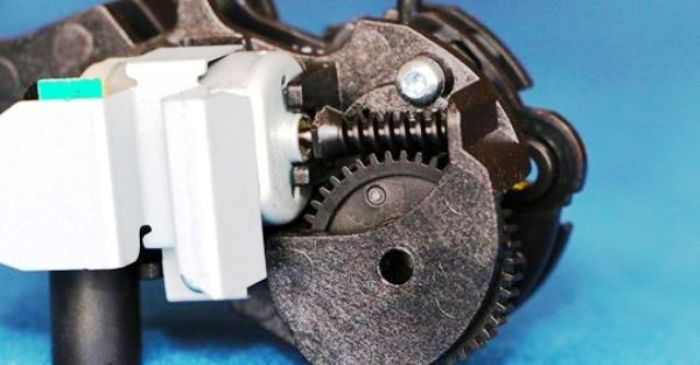
Driving devices utilize gear motors to transfer motor power. They are very essential for a stable and safe operation of the structure being integrated into the wheelset. Conventionally, the major type of power transmission system employed for driving devices is the parallel Cardan drive that commonly uses helical gear motors to perform its function. These motors generate force in the axial direction once the gears have meshed upon a transfer of the torque. As a result, taper roller bearings are also used to bear the corresponding amount of force during power transmission.
Another significant element that affects the performance of the bearing is the adjustment required for axial direction clearance. Poor adjustment for such clearance may lead to serious problems. This is why proper management is so vital. While traditional helical gear motors have been effective for those previously existing applications, it would be difficult for them to meet any future specifications of this driving device.
This is primarily because of the fact that the adjustments needed in noise countermeasures and vibration resistance may result in major concern of excess temperature and seizing if used with the lubricant. Moreover, it would also be difficult to meet the requirements needed for successful bearing life. To effectively deal with this issue, a new driving device has been created to minimize the required maintenance for helical gear motors. This is the double-helical gears and its use means there’s no need for any bearing clearance, ensuring reliability and safety in high-speed operations.
In a normal situation, double helical gear motors don’t generate force when transmitting torque in an axial direction, which allows for the adoption of cylindrical roller bearings. This further leads to improved seizure resistance and longer service life of the bearing. It also helps prevent the need for bearing clearance adjustments while providing low noise and vibration with an improved meshing rate and increased torsion angle. Lastly, there is low noise with the use of cylindrical roller bearings, which means a reduction in noise pollution.
Kommentare