General Principles of Laser Cutting
- vestrainet
- May 7, 2021
- 2 min read
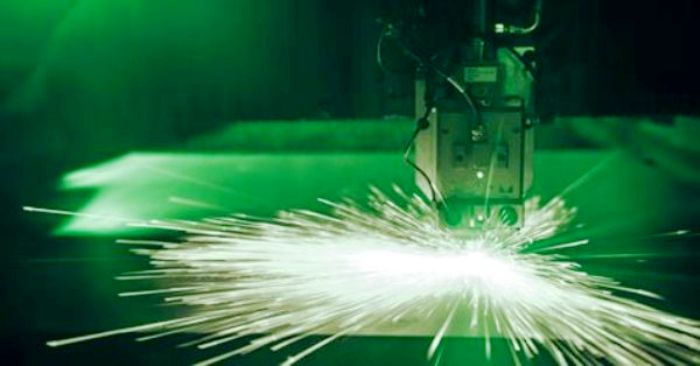
Laser cutting is a non-contact and thermal fabrication process that is widely used to cut both metal and non-metal materials. It has been associated with the great flexibility and high accuracy in cutting a wide range of materials. However, a lot of factors have to be fairly considered when performing this cutting method. These include the laser type, assist gas used, the kind of material to be cut, and the configurations and settings of the laser cutting machine.
While there are different types of laser employed during laser cutting, they all employ the same general principles and basic mechanism of laser cutting. They can be summarized through the following points:
The laser machine generates a high intensity beam of infrared light that is narrowly focused onto the surface of the material to be cut through a lens.
The beam of light heats and produces a highly localized melt that is typically smaller than 0.5mm diameter.
A pressurized gas jet that moves coaxially with the laser beam is used to remove or eject the molten material from the cut. In cutting some materials, the assist gas can both help accelerate the cutting process by doing both physical and chemical works. This is the case with mild steel and carbon wherein a jet of oxygen that is used generates its own heat which further makes the cutting process quicker.
In order to generate the cut, the very localized area of material removal is being moved across the surface of the workpiece. This movement is attained by manipulating the laser focus with the help of CNC (computer numerical control) or by mechanical movement of the workpiece on the axis table.
While those are the basic principles of laser cutting, there are also some hybrid systems in which the workpiece is being moved in one axis while the laser focus is being moved in the other end. In the case of profiling 3D shapes, fully automated and robotic systems are usually employed.
Comments