Fabricating Structural Steel in Toronto: The Benefits of Water-Cooled GMAW Gun
- vestrainet
- Jun 23, 2021
- 2 min read
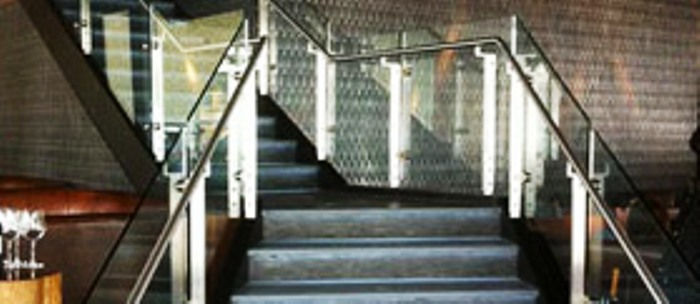
All fabricators of structural steel have been using welding in their processes for centuries now. But with the advances in technology nowadays, they are faced with new choices to make. One in particular is the option to convert from air-cooled to water-cooled gas metal arc welding gun. Under the right application conditions, a water-cooled GMAW gun can help reduce downtime, minimize consumable costs, and increase productivity. The guns operate at higher amperes and duty cycles compared to air-cooled versions. They can work for longer period of time, making them ideal for long arc welds. Despite these promising features, fabricators still need to take a careful analysis of several factors whether their operations would benefit from such conversion.
Apart from amperage and duty cycle requirements, other considerations include the specific application, upfront costs, maintenance and replacement costs, and the potential return on investment (ROI). Also, determining the weld joint design and thickness of the material can help fabricators of structural steel in Toronto to make decisions. For example, preheated heavy plate sections can produce significant amount of radiant heat which can affect how a welding gun cools. The same generated heat can affect the life of the finished structural steel. In this case, a water-cooled gun would be a better choice for the application. In summary, the three key indicators that signify the benefits of switching to a water-cooled gun in a welding operation include:
Overheating of gun temperature
High duty cycle
Excessive consumable usage
These factors are interconnected. When the weld becomes extremely hot, it will automatically result to excessive gun temperature and consumable usage. Generally, water-cooled GMAW guns are most effective to use in high-amperage applications ranging from 350-600 amp. These guns have varying duty cycle capacities and choosing the right one depends on the required amperage rating and cycle time in welding sheet metal and structural steel.
Yorumlar